Leitz DFC®-Extraction hoods
Clean machines, perfect workpieces
Extraction hoods have an enormous influence on the entire production process in machining. It is important that the tool and extraction hood are perfectly matched. Leitz DFC®-Extraction hoods are individually designed and precisely customised to the respective requirements. All processing options, such as profile variants or different material thicknesses, are taken into account. On request, wear can be reduced to an absolute minimum through targeted ceramic coating.
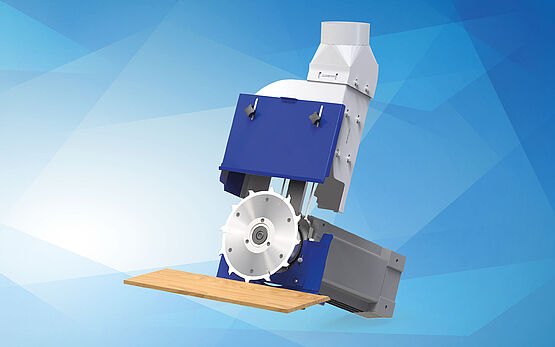
Optimised chip flow: No double cutting, better chip collection and longer tool life.
Fire prevention: Less dust formation and therefore less risk of fire thanks to optimised adjustment of the extraction hoods.
Time and cost savings: Faster tool changes and significantly reduced machine downtimes thanks to ergonomic design.
Sustainability: The DFC®-Extraction hoods offer maximum performance despite reduced energy consumption.
1) Durable extraction hoods thanks to replaceable wear plates
2) Quick tool change thanks to simple assembly
3) Simple spare parts management thanks to stickers and labelling of all components
4) Efficient extraction performance thanks to customised diameters
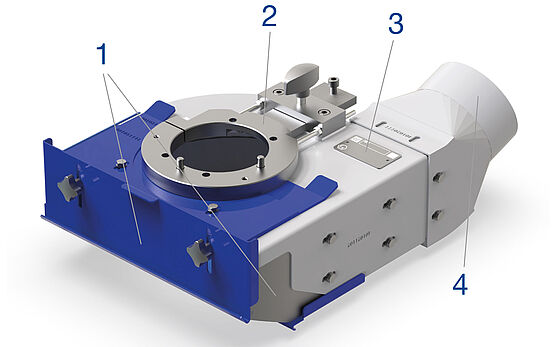
Focus on customer needs
Before a new extraction hood is designed, the conditions on site are measured by a Leitz technician and all needs and requirements are precisely determined. All this information is then taken into account in the design. In this way, each extraction hood is customised to the respective requirements, resulting in a clean machine and perfect workpieces.
Floor production
Floor production
The roots of the Leitz DFC®-Extraction hood are in the flooring industry. A modular system customised to the industry with individual adaptation to the machine environment and profiles leads to fast and efficient project handling.
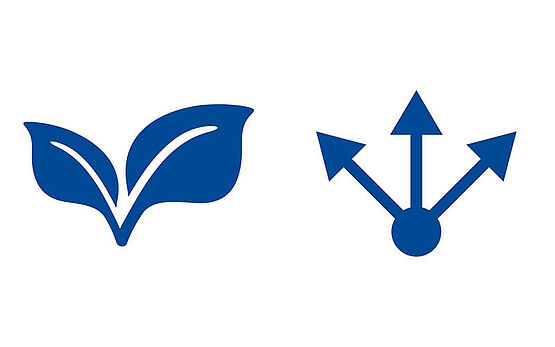
Furniture industry
Furniture industry
Whether for large machining operations or fine profiling and jointing work, the panels must be free of dust and chips in furniture production. Loose edges and pressed-in chips lead to rejects or reworking. These risks can be minimised with perfectly adapted extraction hoods.
Leitz has also repeatedly improved the plate-splitting process with extraction hoods. In addition to the removal of chips, the issue of noise plays a central role here. The LowNoise version delivers significant improvements here!
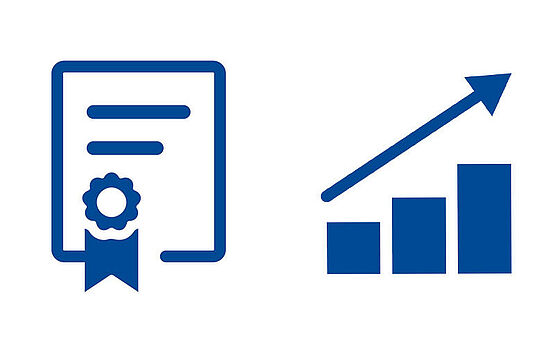
Advanced Materials
Leitz extraction hoods are as diverse as the materials on the market. Whether abrasive fibre cement for facades or soft foam for insulation, each material has different requirements. By using a special ceramic coating for abrasive materials, the lifetime of the extraction hoods can be extended by a factor of more than 10.
Jet nozzle
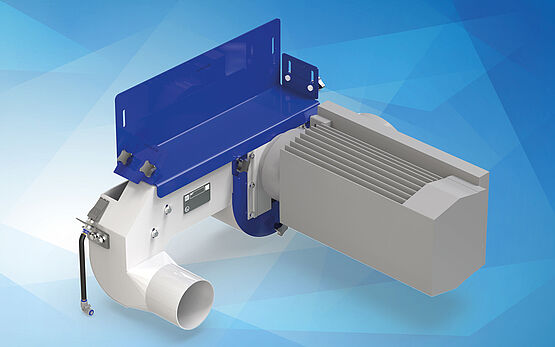
Jet nozzle
For with feed grooving to clean the groove and for special applications, a jet nozzle can be used as an air curtain instead of classic brushes.
LowNoise design
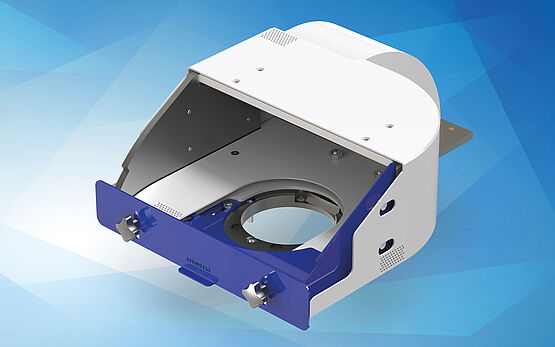
LowNoise design
A special external construction reduces the sound level by up to 5 dB(A).
Lightweight construction
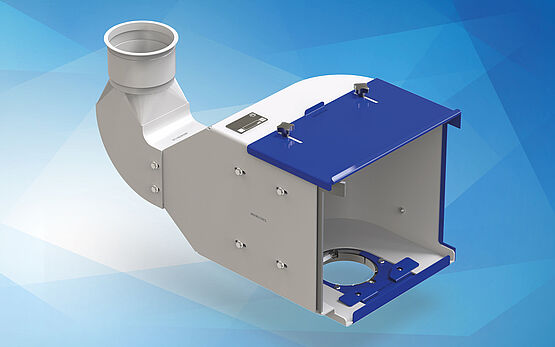
Lightweight construction
Lightweight extraction hoods can be used for large processing thicknesses and non-abrasive materials. An aluminium body and weight-reduced steel parts ensure a weight saving of around 30 %. The focus here is on ergonomics.
Special versions
Every project is individual. Thanks to Leitz‘s many years of experience in the construction of special hoods of all kinds, there is a suitable extraction hood for every requirement.